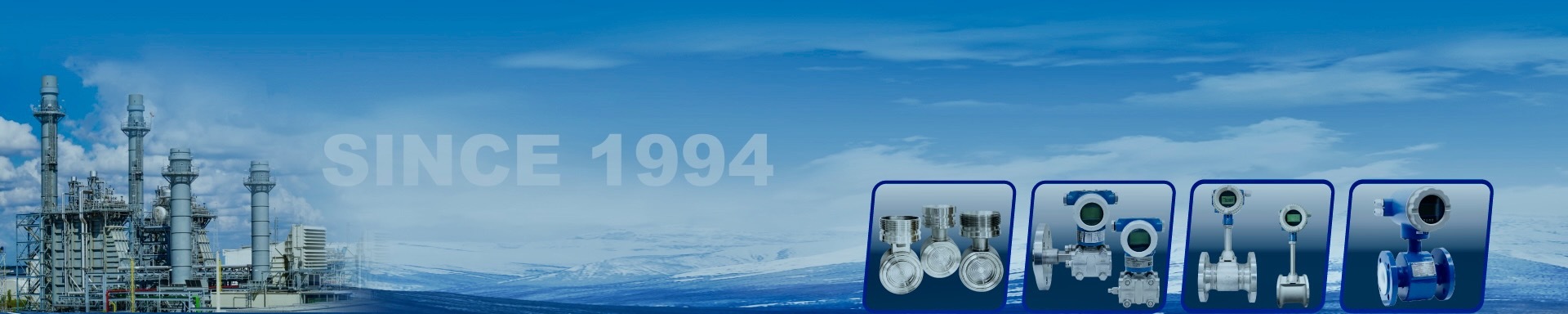
Application of the Pressure Transmitter
A stable and reliable smart pressure transmitter is a powerful guarantee in modern industrial production. Once there is an error in measurement and control in the production process, the result may be that the enterprise stops production or even safety hazards, and the ensuing economic losses will be countless. Therefore, the stability and reliability of the 4-20mA pressure transmitter is to ensure that the whole set of measurement and control system operation of the primary requirements. Typically, pressure transmitter measurements will drift as a result of changes in ambient and static pressure at the measurement site, and this drift can be more severe in the case of micro-pressure or micro-differential pressure measurements. In different working conditions, to get the most accurate measurement data, to ensure production safety, and continuous stability, to ensure that the output product technology meets the standard, the petrochemical industry on the steam pressure transmitter measurement accuracy and stability of the basic requirements.
The petrochemical industry's demand for gauge pressure transmitter is mainly reliability, long-term stability, and high accuracy in three areas. Among them, reliability and many additional needs, such as range ratio, bus type, explosion-proof security, etc., the measuring instrument's structural design, machining process level, and material properties have high requirements. Such as the measurement of chlorine, alkali, and other corrosive media, the measurement and control equipment to have anti-corrosion requirements, which requires the use of tantalum isolation diaphragm or spray anti-corrosion material pressure transmitter or differential pressure transducer. Specific structural design to meet the chemical site installation and use requirements. Again, as ethylene is the leading product of the petrochemical industry, the general process uses a large number of alkaline media (such as sodium hydroxide, and potassium hydroxide), and the reactor temperature is generally 200 ℃ ~ 280 ℃, in the process also need to add hydrogen. Due to the specificity of the process, there are bound to be high corrosion, high temperature, flammable and explosive conditions in the production. When using air pressure transmitter such as pressure or differential pressure, using tantalum or high-temperature silicone oil-filled isolation methods will also greatly improve the practicality and safety of the product.