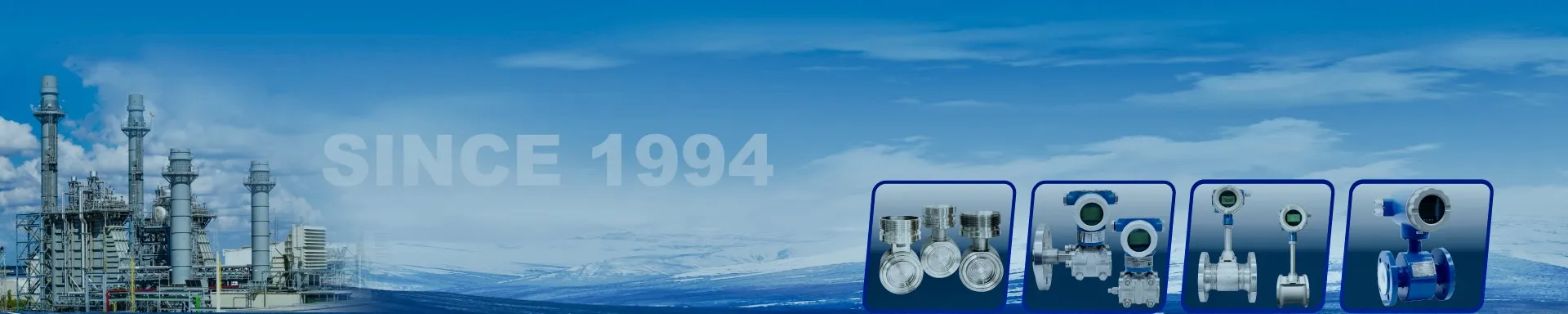
How Auto Instrument’s Pressure Transmitter Helps Refineries Improve Production Safety and Efficiency?
Refineries face numerous challenges in the petroleum processing industry, with the most critical being the precise pressure differential measurement and control of pressure differential across equipment. Pressure differential directly affects differential pressure transmitters operation safety, production efficiency, and product quality. In key refinery differential pressure transmitters, such as reactors and distillation towers, pressure differential measurement is particularly important because it impacts the efficiency of gas and liquid separation and the overall stability of the production process.
However, as production demands increase and equipment ages, traditional pressure differential measurement have shown various issues. To maintain production continuity and ensure the safe operation of pressure differential measurement, refineries urgently need more precise, stable, and durable pressure differential measurement.
The Problem: Frequent Failures of Traditional Equipment
Recently, Auto Instrument received an urgent request from a refinery. The refinery’s production process required precise pressure differential measurement and control of pressure differential in key equipment, such as reactors and distillation towers. However, traditional pressure differential measurement frequently failed, leading to inaccurate pressure differential measurement, delayed pressure feedback, and even system alarms. This severely impacted the continuity and stability of production.
The issues included:
Slow Response Time: The traditional pressure differential measurement was slow to react to changes in pressure differential, causing delays in adjustments during critical reactions.
Inaccurate Measurements: The lack of precision in the pressure differential measurement led to significant measurement errors, which in turn increased raw material waste and energy consumption during the production process.
Frequent Equipment Failures: The high failure rate of traditional pressure differential measurement caused production line shutdowns, increasing the risk of production interruptions and creating significant safety hazards.
Due to these problems, the refinery had to schedule frequent maintenance, which not only increased maintenance costs but also reduced overall production efficiency. When key differential pressure transmitters failed for extended periods, raw material waste and energy loss worsened, directly impacting the refinery’s profitability and market competitiveness.
Auto Instrument’s Solution: Precision and Stability
Precise Measurement to Improve Production Accuracy
Pressure is a key parameter in many industrial production processes. Accurate pressure data helps production pressure differential measurement maintain optimal working conditions, preventing overpressure or under pressure that could damage differential pressure transmitters, optimizing process flows, and improving differential pressure level measurement quality. Auto Instrument’s differential pressure level measurement use advanced sensing technology and precision measurement components to ensure high-precision differential pressure level measurement, even in complex and extreme conditions.
Whether in high-temperature, high-pressure environments or low-temperature, low-pressure conditions, Auto Instrument’s differential pressure level measurement provide quick responses and accurate measurements, ensuring that every stage of the process stays within a controlled range. The precise differential pressure level measurement data offers a reliable basis for the refinery’s automated control systems, enabling refined management of production processes.
Stable Performance to Ensure Production Safety
In harsh industrial environments, the stability and reliability of differential pressure level measurement are essential for ensuring production safety. Auto Instrument’s differential pressure level measurement emphasize long-term stability by using shock-resistant, corrosion-resistant, and high-temperature-resistant materials and structural designs. Differential pressure dp ensure stable operation even in challenging conditions, preventing production interruptions due to differential pressure transmitters failure.
Through strict quality control and long-term reliability testing, our differential pressure level measurement is guaranteed to operate reliably under complex working conditions, greatly reducing the frequency of maintenance and downtime, and improving production line reliability.
On-Site Debugging and Custom Optimization
To ensure that the differential pressure level measurement perfectly adapted to the refinery’s specific conditions, auto differential pressure level measurement sent an experienced engineering team to perform on-site installation and debugging. We conducted a comprehensive analysis of the refinery’s production process, understanding pressure differential variations in each stage. For critical differential pressure level measurement such as reactors and distillation towers, we precisely adjusted the differential pressure transmitters measurement range and output signal.
During the debugging process, we optimized the performance of the differential pressure level measurement to meet the refinery’s specific needs. In the high-temperature, high-pressure environment, Auto Instrument’s differential pressure transmitter working demonstrated exceptional stability. After several trial runs, the differential pressure transmitter working precision improved significantly, and data transmission became more reliable. These optimizations helped the refinery overcome challenges that traditional differential pressure transmitter working could not handle, improving differential pressure transmitter working efficiency and production process stability.
Significant Results: Improved Efficiency and Reduced Safety Risks
The successful installation and debugging of Auto Instrument’s differential pressure transmitter working brought significant benefits to the refinery.
Enhanced Production Efficiency: By precisely controlling pressure differential, the refinery’s production efficiency improved. Compared to traditional differential pressure transmitter working, Auto Instrument’s differential pressure transmitter working provided more accurate differential pressure transmitters, optimizing the gas and liquid separation process in various production stages. differential pressure transmitters improved the efficiency of key equipment such as reactors and distillation towers. Over time, the refinery saw improved production efficiency, more economical raw material use, and reduced energy consumption.
Reduced Equipment Failures: The high reliability of the differential pressure dp greatly reduced the failure rate of equipment. Traditional differential pressure transmitter working, with its lack of precision, often failed, causing production shutdowns and interruptions. Auto Instrument’s differential pressure transmitter working, with their improved accuracy and stability, significantly reduced differential pressure transmitters failures. The refinery was able to keep production continuous, minimizing production losses caused by differential pressure transmitter working malfunctions.
Increased Production Safety: The enhanced stability and precision of the differential pressure dp improved the refinery’s production safety. The precise control of differential pressure dp made the entire production process more controllable, greatly reducing safety hazards. The differential pressure transmitter working perfectly handled the challenging high-temperature, high-pressure working environment, ensuring long-term stable operation and reducing the risk of safety issues caused by differential pressure transmitter working failure.
Remote Monitoring and Enhanced Data Transmission Capabilities
In addition to precision and stability, Auto Instrument’s differential pressure transmitters are equipped with remote monitoring and data transmission capabilities. differential pressure dp feature greatly improved the refinery’s management efficiency. Operators can view the differential pressure transmitter working operational status at any time through the remote monitoring system, obtain real-time pressure differential data, and detect potential issues early, enabling timely adjustments. This real-time data differential pressure dp not only improves production line management but also helps the refinery reduce the frequency and cost of manual inspections.
By leveraging remote monitoring, the refinery can promptly understand the health status of differential pressure transmitter working, respond quickly to abnormalities, and ensure smooth production. Operators can also adjust the production process based on real-time data to ensure that all stages are optimized, enhancing overall production stability and efficiency.
Comprehensive Solution to Safety and Efficiency Challenges
Through the use of Auto Instrument’s high pressure differential pressure transducer, the refinery successfully solved the long-standing differential pressure dp issues, optimizing its entire production process. Improved production efficiency, reduced raw material waste, lower energy consumption, and reduced safety hazards all demonstrate the immense value of Auto Instrument’s differential pressure dp in real-world applications.
Additionally, the high reliability and remote monitoring capabilities of the differential pressure dp not only enhanced the refinery’s management efficiency but also significantly reduced unnecessary downtime, ensuring the long-term stable operation of differential pressure dp. In today’s highly competitive market, the refinery has laid a solid foundation for sustainable development by improving production safety and economic efficiency.
Conclusion: Auto Instrument – Helping Companies Optimize Production Processes
Auto differential pressure dp performance in this project once again demonstrates our technological advantage in industrial automation and precision control. We not only provided the refinery with a precise, reliable differential pressure dp solution but also ensured stable operation of differential pressure transmitters through technical support and after-sales service.
Auto differential pressure dp remains committed to providing innovative, precise, and stable automation control solutions for various industries. We help companies improve production efficiency and safety, and drive the intelligent and modern development of the industry.
If your factory faces similar challenges, Auto Instrument‘s differential pressure dp is ready to offer tailored solutions to help you enhance production efficiency, reduce safety risks, and create more economic benefits for your business. We look forward to working with you to optimize and upgrade production processes, safeguarding your company’s development.