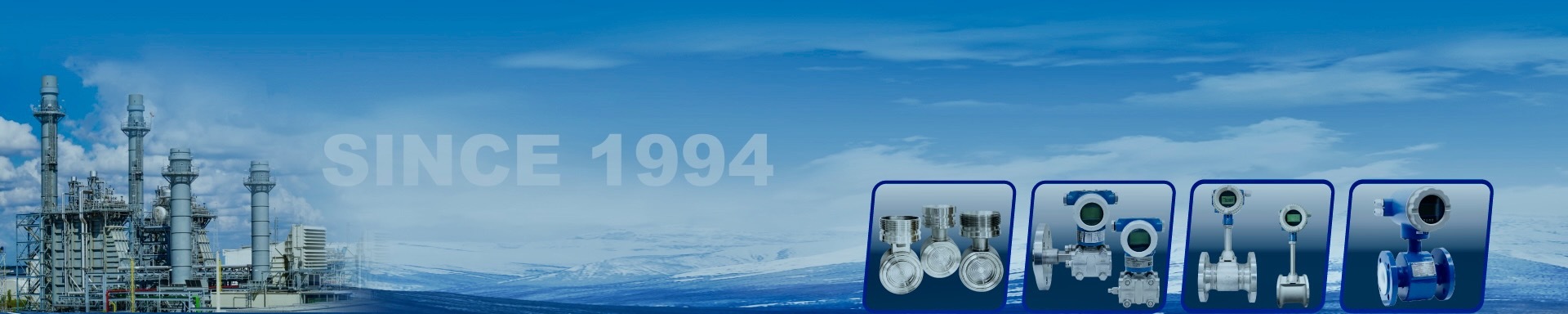
Differential Pressure Transmitter - Pipeline Pressure Monitoring
In industrial production, the piping system is a very important component. The pressure transmitter differential is a commonly used pressure sensor that can measure the pressure difference between two different locations. In this article, we will discuss in depth how the 3051 differential pressure transducer realizes the monitoring of conveying pipeline pressure.
The dp transmitter is a measuring instrument used to measure the pressure difference between two different locations. The pressure transmitter differential converts the pressure difference in the pipeline into an electrical signal, thus realizing the monitoring of pressure. The digital differential pressure transmitter is composed of a pressure sensor, a signal conditioner, and a signal converter.
The 3051 dp transmitter is a commonly used pressure transmitter differential. The 3051 dp transmitter has many advantages. The 3051 pressure transmitter differential can measure pressure with high accuracy. The 3051 differential pressure transducer can provide a variety of output signals, such as 4-20mA, HART, etc. The 3051 differential pressure transducer can be programmed on-site to achieve a wide range of parameter adjustments to adapt to different application environments. The 3051 dp transmitter adopts various protection measures, such as over-voltage and over-current protection. It makes the 3051 dp transmitter highly reliable. The 3051 dp transmitter is small and lightweight, easy to install and maintain.
So, what are the specific steps for the 3051 differential pressure transducer to monitor the pressure of the transmission pipeline?
First, install the 3051 digital differential pressure transmitter on the conveying pipeline. Generally speaking, the digital differential pressure transmitter should be installed between two bends in the pipeline to obtain an accurate pressure difference. During installation, it should pay attention to the direction and position of the digital differential pressure transmitter.
Next, connect the 3051 dp transmitter to the circuit of the control system. Normally, the output signal of the pressure transmitter differential should be input to the control system through a cable. In addition, it needs to set the parameters of the control system for calibration of the differential pressure transducer and reading of the output signal.
After installation, it is necessary to calibrate to ensure that the pressure values measured by the dp transmitter are accurate. The calibration process consists of a zero calibration and a full-scale calibration. When performing calibration, the air/fluid supply to the pipeline should be disconnected first so that the pressure inside the pipeline is zero, and then zero calibration should be performed. Next, adjust the gas/liquid pressure in the pipeline to the maximum value, and calibrate the full-scale calibration.
Next, the dp transmitter is ready to monitor the pressure in the delivery pipeline. The differential pressure transmitter will convert the pressure difference into an electrical signal output. Then, the control system reads the output signal and monitors the pipeline pressure.
The following is an example of pressure monitoring of a conveyor pipeline using the 3051 differential pressure transmitter.
One of our customers is from a petrochemical company. In the transportation pipeline system of this enterprise, the oil in the pipeline has different densities and viscosities, which leads to a relatively large pressure change in the pipeline. To monitor the pressure in the pipeline in real-time, the customer purchased our Auto 3051differential pressure transducer. After calibrating and adjusting the parameters of the 3051 dp transmitter, it was put into use and successfully realized the monitoring of pipeline pressure.
In conclusion, the 3051 digital differential pressure transmitter is an effective instrument for monitoring the pressure in the pipeline. The 3051 dp transmitter can help companies find and deal with abnormalities promptly to ensure the safety of the pipeline system.