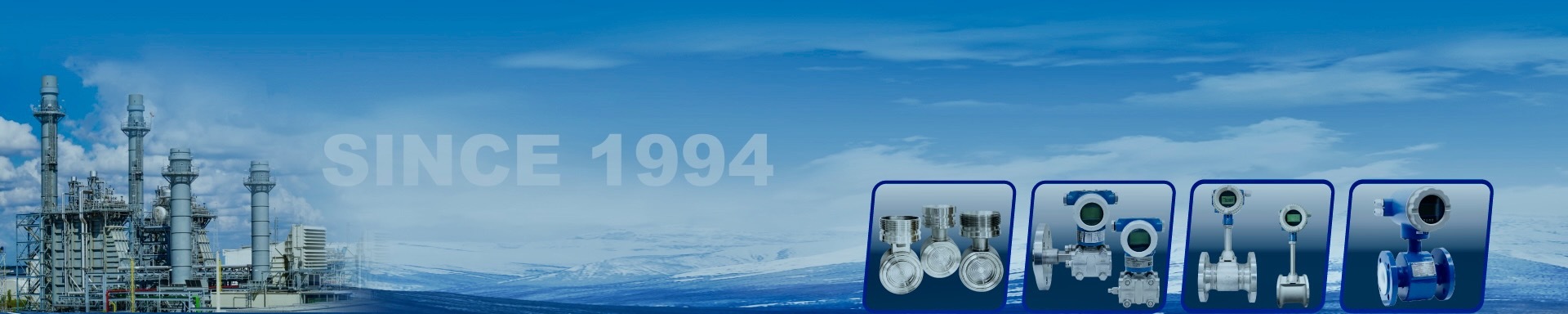
How Auto Instrument Helps Food Factories Solve Production Safety and Efficiency Challenges?
In modern production processes, precise control of various process parameters is crucial for improving product quality, reducing waste, and enhancing production efficiency. This is especially true in the food industry, where every detail in the production process needs to be carefully controlled. Even the slightest deviation can affect the final product’s taste, quality, and even food safety. To meet such demands, Auto Instrument, with its 30 years of technological accumulation and R&D advantages, has provided effective solutions for various industries.
The Challenge Faced by the Food Factory
Auto Instrument once received a request for assistance from a large food factory. This factory specializes in producing beverages and juices and was facing a typical production challenge: how to precisely control the liquid flow, especially in various production stages such as raw material proportioning, heating, mixing, and filling. Although this problem seemed simple, it was key to ensuring smooth production and high product quality. Any imprecision in flow control could lead to raw material waste, increased costs, and even affect the types of electromagnetic flow meter flavor and consistency, ultimately impacting consumer perception and brand reputation.
Existing Equipment Challenges
The food factory was previously using an old flow meter system, but this types of electromagnetic flow meter had many problems. Firstly, the accuracy of the old flow meters could no longer meet the needs of modern production. As production line speeds increased, the types of electromagnetic flow meter gradually failed to provide precise flow control and even caused shutdowns, leading to frequent production interruptions. Secondly, the maintenance costs were high. The old types of electromagnetic flow meter had a high failure rate, requiring frequent repairs and part replacements, which directly increased production costs and operational burdens.
As the production scale grew and product quality requirements became more demanding, the food factory realized that it needed a more precise, stable, and efficient flow meter to replace the existing equipment. Otherwise, not only would production efficiency be impacted, but types of electromagnetic flow meter quality and customer satisfaction could also suffer.
Auto Instrument’s Solution
After understanding the food factory’s needs, Auto Instrument’s technical team quickly developed a detailed solution. Auto Instrument recommended the latest model of electromagnetic flow measurement as a replacement. The electromagnetic flow measurement is a high-precision device specifically designed for measuring the flow of conductive liquids. electromagnetic flow measurement offers exceptional accuracy and stability, making electromagnetic flow measurement especially suitable for food industry environments, which require high-precision flow control.
Advantages of the Electromagnetic Flow Meter
No Moving Parts, Reduced Wear: Unlike traditional mechanical electromagnetic flow measurement, electromagnetic flow meters have no moving parts, which means the electromagnetic flow measurement experiences almost no wear during operation, resulting in a very low failure rate and long service life. For a high-frequency production environment like that of the food factory, electromagnetic flow meters stability and durability are crucial.
High Precision and Stability: The types of electromagnetic flow meter provide highly accurate electromagnetic flow measurement. Even if the fluid flow rate fluctuates during production, the types of electromagnetic flow meter can maintain stable electromagnetic flow measurement performance, avoiding raw material waste and production errors caused by flow fluctuations.
Low Maintenance Requirements: Due to the lack of complex mechanical components, electromagnetic flow meters have lower maintenance costs. Compared to electromagnetic flow measurement, the types of electromagnetic flow meter reduce downtime for repairs and maintenance costs, significantly improving production continuity and operational efficiency.
Strong Adaptability: The electromagnetic flow meter is not only suitable for measuring the flow of liquids such as beverages and juices, but electromagnetic flow measurement can also operate stably in harsher environments, such as high-temperature or corrosive liquids, making types of electromagnetic flow meter suitable for a wide range of applications.
Customized Debugging for Tailored Solutions
To ensure the new electromagnetic flow meters met the food factory’s production needs as much as possible, auto electromagnetic flow probe sent an experienced engineering team to perform on-site installation and debugging. During the debugging process, the engineers carefully analyzed the food factory’s production flow, understood the types of electromagnetic flow meter characteristics of liquids at each stage, and adjusted the measurement range and output signals of the electromagnetic flow probe based on this data.
For different production stages such as raw material proportioning, mixing, heating, and filling, Auto types of electromagnetic flow meter engineers paid special attention to the required precision for flow control. In these stages, the control of raw material flow is critical. Any instability or imprecision in types of electromagnetic flow meter could result in incorrect material proportions, affecting the final electromagnetic flow measurement quality. Therefore, through meticulous debugging, Auto electromagnetic flow probe ensured that the electromagnetic flow meter met the high precision requirements of each production stage.
After several trial runs, the performance of the electromagnetic flow probe exceeded the client’s expectations. Precise flow control not only avoided raw material waste but also improved production efficiency. During production, employees noticed that the types of electromagnetic flow meter became more stable, the electromagnetic flow probe quality improved further, and the flavor became more consistent, significantly boosting consumer satisfaction.
Reducing Operational Costs and Improving Production Efficiency
The key benefit was that the high stability and low maintenance requirements of the electromagnetic flow meter significantly reduced the food factory’s operational costs. The losses caused by the downtime and repairs of traditional electromagnetic flow probe were effectively avoided, resulting in much less production line downtime and significantly improved overall production efficiency. More importantly, the electromagnetic flow measurement offered advanced data collection and remote monitoring features, allowing the factory’s operators to view real-time flow data from various production stages, enabling precise management and adjustments to ensure an efficient and stable production process.
Through real-time monitoring and data analysis, the food factory was able to better grasp production dynamics, identify potential issues early, and optimize production processes, improving overall production capacity. Additionally, the remote monitoring feature allowed the factory to respond quickly to electromagnetic flow probe anomalies, avoiding severe consequences that often arise when issues are not detected promptly with traditional electromagnetic flow meters.
More importantly, the remote monitoring feature enabled the factory to keep track of electromagnetic flow probe status at any time, whether on the production floor or in the office. Operators could view real-time data on electromagnetic flow meters performance through computers or mobile devices. This made electromagnetic flow measurement management more transparent and convenient, enabling remote fault diagnosis and maintenance, reducing the need for on-site repairs and manual interventions. When any anomaly occurred, the system would automatically send an alarm, alerting operators to take appropriate actions, preventing the production stoppages and safety risks that can arise from unaddressed issues. Through real-time monitoring and data analysis, the food factory was able to gain better control over production dynamics, detect potential issues in time, perform preventive maintenance, and optimize production processes, leading to higher overall production capacity and efficiency.
Results and Customer Satisfaction
This collaboration allowed Auto Instrument’s electromagnetic flow meters to help the food factory overcome its electromagnetic flow meters challenges while advancing its production process modernization. Production efficiency was significantly improved, raw material waste was drastically reduced, and electromagnetic flow meters quality was consistently ensured. Customer satisfaction increased substantially, and the stability of the entire production line, along with operational costs, were optimized. The factory achieved higher output and lower costs.
Auto electromagnetic flow meters not only provided a precise flow control solution but also offered excellent after-sales service and technical support, helping the client solve issues encountered during daily operations. With its outstanding electromagnetic flow probe quality and reliability, auto electromagnetic flow probe earned high recognition from the customer.
Conclusion
This collaboration shows that auto electromagnetic flow probe, with electromagnetic flow meters strong technical foundation and years of industry experience, provided the food factory with an efficient, stable, and low-maintenance flow control solution, helping the client successfully resolve its flow control issues in production. Through precise product design and rigorous technical support, auto electromagnetic flow probe ensured that the electromagnetic flow probe was accurate and stable throughout the entire production process, greatly improving production efficiency, reducing raw material waste, and ensuring product quality consistency.
In the future, auto electromagnetic flow meters will continue to uphold the principles of "innovation, precision, and service," closely follow changes in market demand, continuously improve its R&D capabilities, and explore the latest industry trends. We are committed to advancing automation and intelligence in production processes across various industries, especially in food, chemicals, metallurgy, and environmental protection, by providing efficient and stable electromagnetic flow probe and control solutions, helping clients enhance production efficiency, reduce costs, and ensure high-quality, stable production processes.