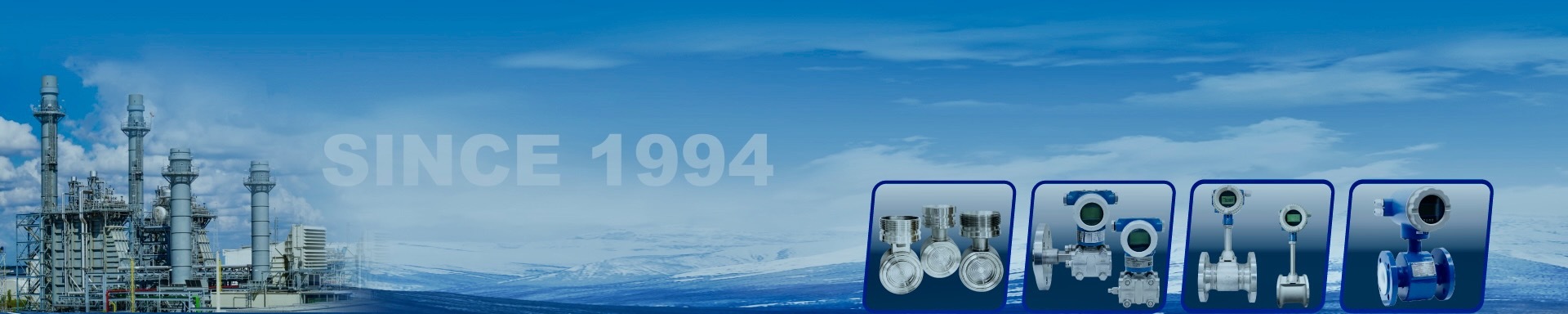
How AUTO Instruments Helps a Food Factory Solve Unstable Level Measurement Issues?
Background: A local food factory faced frequent issues with the level measurement equipment used on their production line, especially under conditions where the liquid level was unstable, materials adhered to surfaces, and temperature fluctuations were significant. Traditional float level sensors and capacitive level sensors were unable to provide stable readings, leading to production stoppages and material waste. The factory had strict requirements for the precision, stability, and reliability of measurement instruments, particularly when dealing with viscous or easily crystallized liquids. Traditional equipment could not cope with these challenges, resulting in low production efficiency and even affecting product quality.
AUTO Instruments' Intervention: After understanding the challenges faced by the food factory, AUTO Instruments dispatched a professional technical team to have one-on-one discussions with the factory engineers. They thoroughly analyzed the production process and specific operating conditions. Based on the data and on-site situation, AUTO recommended its self-developed guided wave radar type level transmitter, which is ideal for high-viscosity and easily crystallizing liquids, offering high-precision and stable level measurement even in complex environments.
Solution: AUTO provided the food factory with a customized radar level meter solution, which included the following key features:
1. Anti-interference Design: To address interference from agitators, liquid level fluctuations, and other factors, AUTO’s radar type level indicator features a high signal-to-noise ratio design, ensuring the level measurement remains unaffected by material fluctuations.
2. Anti-adhesion and Corrosion-resistant Antenna: The radar level meter’s antenna is made from PTFE material, which effectively prevents material adhesion, reduces maintenance frequency, and provides excellent corrosion resistance, making it suitable for the various liquids in the food industry.
3. High Temperature and Pressure Resistance: The equipment can operate stably under high temperatures (above 80°C) and pressure conditions, ensuring that environmental fluctuations in food production do not affect its performance.
4. Precise Measurement: The guided wave radar level meter has an accuracy of up to ±15mm, ensuring precise liquid level measurement, whether it’s syrup, juice, or other viscous liquids, maintaining stable and accurate readings.
Results: After installing and commissioning AUTO’s radar level meters, the food factory’s level measurement issues were fundamentally resolved:
1. Improved Stability: The equipment operated stably under complex conditions, reducing production downtime caused by liquid level fluctuations.
2. Reduced Maintenance Costs: With the radar level meter’s anti-adhesion antenna, maintenance intervals were significantly extended, reducing costs associated with cleaning and repairs.
3. Increased Production Efficiency: Precise level measurement effectively reduced raw material waste, improving production line efficiency and product consistency.
4. Quality Assurance: Accurate liquid level monitoring ensured precise ingredient dosing and proportioning during production, guaranteeing product quality and taste.
5. Labor Savings: By automating level measurement, the radar level meter helped save on labor costs, improving worker efficiency.
Summary: By providing a tailored radar level meter solution, AUTO Instruments not only solved the food factory’s issues with unstable level measurement and difficult maintenance but also improved production efficiency, reduced operational costs, and ensured product quality. This solution was highly appreciated by the factory and further solidified AUTO Instruments’ market position in the food industry.