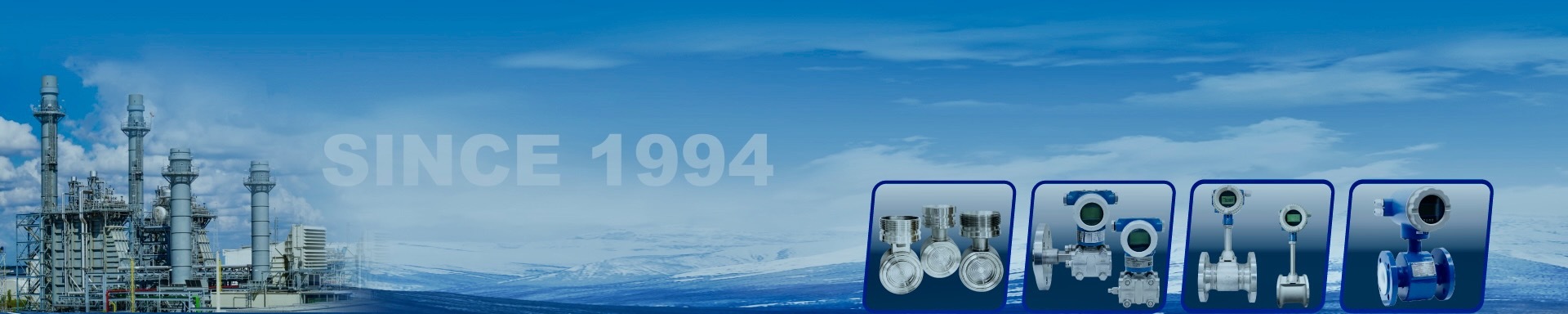
Why Does Pressure Transmitter Measurement of Oxygen Require Degreasing and De-oiling Treatment?
When a Transmitter pressure gauge is used to measure oxygen, it requires degreasing and de-oiling treatment. This is due to the nature of oxygen, which may react dangerously with oils and other organic substances under certain conditions, potentially causing explosions. Below is a detailed explanation of the reasons for this treatment and the applicable scenarios.
1. Properties of Oxygen and Risk Analysis
1.1 Strong Oxidizing Properties of Oxygen: Oxygen is a strong oxidizing agent that can rapidly react with certain oils and organic substances.
When oils are present, these oxidation reactions may release a large amount of heat quickly, causing local high temperatures, which may lead to fire or explosion.
1.2 Increased Risks in Pressurized Environments: When the capacitance pressure transmitter is used in high-pressure oxygen environments, the oxidizing activity of oxygen is significantly enhanced, increasing the risk of contact with oils.
1.3 The Role of Particle Contaminants: In addition to oils, certain solid particles (e.g., rust or dust) can act as catalysts for oxidation reactions, further increasing the risk.
2. Purpose of Degreasing and De-oiling
2.1 Preventing Oxidation Reactions: By degreasing and de-oiling, oils or organic materials on the surface or inside the sensor channels are removed to prevent contact between oxygen and oils.
2.2 Enhancing Measurement Safety: Processed equipment can effectively reduce the risk of accidents caused by oils, improving system reliability and safety.
2.3 Ensuring Measurement Accuracy: Residual oils may adsorb particles or cause blockages in the internal channels, affecting sensor performance and measurement accuracy.
3. Specific Methods for Degreasing and De-oiling
3.1 Chemical Cleaning: Use specialized degreasers (such as trichloroethylene, alcohol, etc.) to clean the sensor.
3.2 Ultrasonic Cleaning: Perform ultrasonic cleaning of the sensor components to remove stubborn oils.
3.3 High-temperature Drying: After degreasing and cleaning, use drying to remove any residual cleaning agents and moisture.
3.4 Verification and Inspection: After de-oiling, use ultraviolet lamps, residual oil test strips, or oxygen exposure tests to verify the effectiveness of the treatment.
4. When is Degreasing and De-oiling Required?
Degreasing and de-oiling treatment should be especially noted under the following conditions:
4.1 The Medium is Pure Oxygen or High Oxygen Concentration Gas: In high-purity oxygen (typically purity >99%) or high-concentration oxygen environments, the oxidizing activity of oxygen is significantly enhanced.
4.2 High System Pressure: When the oxygen pressure in the system is high (e.g., >1 MPa), the reactivity of high-pressure oxygen increases significantly, and strict degreasing is required.
4.3 Medical and Aerospace Applications: In medical equipment (e.g., ventilators) and aerospace environments, oxygen safety requirements are very high, and ensuring there is no oil contamination is essential.
4.4 High Environmental Temperature: If the measurement environment is at a high temperature (e.g., >60°C), elevated temperatures accelerate oxidation reactions.
4.5 Presence of High-Sensitivity Components: When there are components in the system that are sensitive to contamination or reaction, such as precision valves or coated materials.
5. Summary
Degreasing and de-oiling treatment for oil transmitters measuring oxygen is crucial to avoid reactions between oils and oxygen, enhancing system safety. The specific treatment requirements depend on factors such as oxygen purity, pressure, temperature, and application scenarios. In high-purity, high-pressure oxygen systems, as well as in high-safety areas like medical and aerospace applications, strict degreasing and de-oiling treatment is required. In ordinary air or conventional applications, such treatment may not be necessary.